Lub wypełnij formularz na stronie
Pomoc w doborze
Wypełnienia nasypowe
Nasady nieregularne dzielą się na stacjonarne i mobilne, a nasady zwykłe na nasady blokowe i nasady z indywidualną stylizacją.
Stacjonarne nasady masowe mają kształt pierścieniowy, cylindryczny, siodełkowy, kulisty i inne. Udoskonalenie stacjonarnych nasad masowych uzyskuje się głównie poprzez modyfikację znanych konstrukcji, na przykład poprzez zwiększenie liczby giętych elementów lub zmianę stosunku wysokości i szerokości pakowanego korpusu.
Korpusy uszczelniające dysz ruchomych są kuliste, cylindryczne, spiralne, pierścieniowe, pryzmatyczne, sześcienne, mogą być wydrążone, pełne lub perforowane.
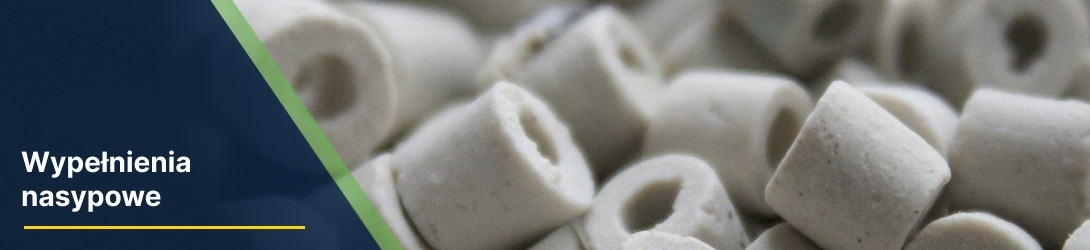
Urządzenia z upakowanym stykiem jako narzędzie do intensyfikacji procesów wymiany ciepła i masy na granicy faz i w jej pobliżu poprzez rozwinięcie powierzchni styku i poprawę mieszania przepływów znajdują zastosowanie w procesach wymiany ciepła i masy, które znalazły szerokie zastosowanie w przemyśle. Procesy stosowane na największą skalę to absorpcja, rektyfikacja i chłodzenie wyparne wody. Absorpcja - selektywna absorpcja gazów lub par przez absorbent cieczy (absorbent). Ten proces, w którym biorą udział fazy gazowa i ciekła, polega na przejściu substancji z fazy gazowej lub gazowej do cieczy. Proces odwrotny to uwolnienie zaabsorbowanego gazu lub pary z absorbera – desorpcja. Rozróżnij absorpcję fizyczną i chemisorpcję. W absorpcji fizycznej rozpuszczaniu gazu nie towarzyszy reakcja chemiczna. Przy 15 absorpcji chemicznej zaabsorbowany składnik wchodzi w reakcję chemiczną w fazie ciekłej. W przeciwieństwie do rektyfikacji proces absorpcji jest głównie jednokierunkowy. odpowiednie składniki są ekstrahowane z gazu i praktycznie nie przechodzą z absorbenta do fazy gazowej. Podobną sytuację obserwuje się podczas desorpcji. W przemyśle proces bezpośredni (absorpcja) i proces odwrotny (desorpcja) są najczęściej stosowane w połączeniu: absorpcja, a następnie desorpcja. Ta kombinacja umożliwia ponowne użycie absorbentu i wyizolowanie zaabsorbowanego składnika w czystej postaci. W tym celu roztwór po absorberze kieruje się do desorpcji, gdzie w wyniku odciążenia lub ogrzewania zaabsorbowany składnik jest uwalniany, a zregenerowany absorbent wraca do absorpcji. W takim cyklicznym procesie rozpuszczalnik nie jest zużywany, ale cały czas krąży w układzie absorber-adsorber-absorber. W chemisorpcji absorbent jest regenerowany metodami grzewczymi lub chemicznymi.
W technologii chemicznej połączenie absorpcji i desorpcji wykorzystuje się najczęściej do:
- separacji z mieszanin gazów różnego pochodzenia składników wyjściowych, które są następnie dostarczane do syntezy;
- na etapie przygotowania do syntezy gazu źródłowego lub mieszanin gazów (odwodnienie, usunięcie szkodliwych zanieczyszczeń);
- oddzielenie cennych składników z mieszaniny gazowej uzyskanej w wyniku reakcji lub rozkładu termicznego;
- usuwanie szkodliwych zanieczyszczeń ze spalin (oczyszczanie sanitarne) z późniejszym wykorzystaniem wydobytych substancji;
- wychwytywanie cennych substancji ze spalin w celu zapobiegania ich utracie, a także ze względów środowiskowych. 16 Z powyższego widać, że połączenie absorpcji i desorpcji, jako operacja technologiczna, jest szeroko stosowane na różnych etapach procesów produkcyjnych.
W niektórych przypadkach stosuje się tylko absorpcję (bez późniejszej desorpcji):
- w celu uzyskania produktu docelowego poprzez absorpcję gazu przez ciecz;
- w celu oczyszczenia gazu z niepożądanych zanieczyszczeń, jeżeli absorbent i produkt odzyskiwany są produktami odpadowymi lub są tak tanie, że regeneracja absorbentu nie jest ekonomicznie opłacalna.
W procesach absorpcyjnych zaprojektowanych do realizacji powyższych zadań technologicznych stosuje się głównie upakowane urządzenia kontaktowe. Rektyfikacja jest stosowana nie mniej powszechnie niż absorpcja. Rektyfikacja [7] to rozdzielenie ciekłej mieszaniny na składniki poprzez przeciwprądowe oddziaływanie strumieni pary powstającej podczas parowania i cieczy powstałej w wyniku kondensacji pary. Proces ten obejmuje wielokrotnie powtarzane przejścia substancji z fazy ciekłej do fazy gazowej i odwrotnie. W starożytności znany był jednorazowy akt parowania, w którym składnik głównie lotny przechodzi w parę, a następnie skrapla się - destylacja. Otrzymał znaczący rozwój, gdy nauczył się ekstrahować alkohol z produktów fermentacji materiałów zawierających skrobię i cukier. W przeciwieństwie do absorpcji, podczas rektyfikacji proces ten nie przebiega jednokierunkowo z każdym pojedynczym aktem. Podczas parowania wraz ze składnikiem lotnym odparowuje pewna ilość mało lotnego składnika. Dlatego za pomocą jednego aktu nie można uzyskać czystego lotnego produktu. Potrzebujesz wielokrotnych powtórzeń jednego aktu. Z tego powodu do realizacji destylacji 17 wymagane są duże koszty energii, znacznie wyższe niż przy rozdzielaniu absorpcyjnym. Jednak ze względu na to, że dobierając wymaganą liczbę kolejnych pojedynczych aktów można wyizolować z mieszaniny produkt o dostatecznie wysokiej czystości, rektyfikacja znalazła jednak szeroki rozkład. Proces rektyfikacji może być zorganizowany okresowo lub w sposób ciągły. Przy wykonywaniu ciągłej rektyfikacji mieszanin binarnych może to być mieszanina składników o nieograniczonej wzajemnej rozpuszczalności, mieszanina składników o niskiej temperaturze wrzenia lub mieszanina azeotropowa. Aby oddzielić mieszaniny składników o niskiej temperaturze wrzenia, często stosuje się destylację ekstrakcyjną, w której do mieszaniny dwuskładnikowej dodaje się trzecią część - środek rozdzielający, który może znacznie zwiększyć względną lotność zasady komponentów. Mieszaniny azeotropowe są rozdzielane przez destylację azeotropową. Najtrudniejsza jest rektyfikacja mieszanin wieloskładnikowych. Istnieją różne schematy jego realizacji.
Destylacja próżniowa służy do rozdzielania mieszanin termolabilnych. Rektyfikacja ma szczególne znaczenie w tych gałęziach przemysłu, w których konieczne jest całkowite rozdzielenie płynnych mieszanin na czyste składniki lub ich grupy. Do realizacji procesów rektyfikacji stosuje się głównie urządzenia stykowe płytowe. Powszechne stosowanie wypełnień w procesach destylacji, pomimo prostoty urządzenia i stosunkowo niskiego kosztu, jest utrudnione przez ich mniejszą wydajność ze względu na nierównomierny rozkład przepływów pary i cieczy w przekroju warstwy wypełnienia. Dlatego kolumny destylacyjne z wypełnieniem o średnicy większej niż 2-3 m są rzadkością w zakładach chemicznych. Jednakże wypełnienia są niezbędne do destylacji substancji termolabilnych, ponieważ tylko wypełnienia siatkowe są w stanie zapewnić bardzo niski opór hydrauliczny urządzenia do przenoszenia masy, który jest niezbędny do prowadzenia procesu rektyfikacji w próżni. 18 Urządzenia kontaktowe są również szeroko stosowane do chłodzenia gazów wodą i cieczy (głównie wody) powietrzem lub gazami (jeśli mogą być nasycone parą chłodziwa) z bezpośrednim kontaktem fazowym
Jeżeli suszenie gazów związane z przenoszeniem wody z gazu do fazy ciekłej, zgodnie z jego przeznaczeniem technologicznym, jest w całości związane z procesami wymiany masy, to chłodzenie wody powietrzem, któremu również towarzyszy przenoszenie wody natomiast od fazy ciekłej do fazy gazowej, zgodnie z przeznaczeniem technologicznym, odnosi się do procesów wymiany ciepła. Wymiana ciepła w bezpośrednim kontakcie przebiega znacznie wydajniej niż w przypadku zastosowania urządzeń wymiany ciepła, gdzie przepływy poruszające się w przeciwprądzie są oddzielone powierzchnią wymiany ciepła (ścianką). Opór cieplny tej ściany, a także zanieczyszczenia, które nieuchronnie gromadzą się po obu jej stronach, zmniejszają efektywność wymiany ciepła. Bardzo ważne jest, aby podczas bezpośredniego kontaktu faz odprowadzana była znaczna ilość ciepła w wyniku odparowania części cieczy do fazy gazowej. Wszystko to razem zapewnia wysoką wydajność chłodzenia. Jednak powtarzamy, jest to dopuszczalne tylko wtedy, gdy technologia pozwala na nasycenie gazu parą cieczy. Takie nasycenie jest całkiem akceptowalne w przypadku chłodzenia wyparnego wody obiegowej w chłodniach kominowych, w których stosuje się regularne wypełnienie. Oczywiście pożądane jest, aby parowanie było minimalne z dwóch powodów. Po pierwsze, ze względu na utratę cyrkulacji wody, często poddawana wstępnej obróbce chemicznej w celu zmniejszenia zawartości soli w cieczy. Po drugie ze względu na nieuniknione nawilżenie i zanieczyszczenie basenu powietrza w rejonie chłodni kominowych. W tym celu wieże chłodnicze są wyposażone w specjalne urządzenia, które minimalizują przenoszenie wody przez kropelki z wież chłodniczych.
Obszary i zakres zastosowania Zakłady chemiczne można rozpoznać z daleka po charakterystycznych filarach. Ich wysokość sięga czasem 100 m, średnica to kilka metrów. To w nich zachodzą procesy wymiany masy – absorpcji i rektyfikacji. W całkowitym wolumenie wyposażenia technologicznego zakładów chemicznych zużycie metalu na takie wyposażenie w niektórych przypadkach sięga 60%. Znaczna część tego sprzętu spada na urządzenia pakujące. Kolumny z wypełnieniem są szeroko stosowane w wielu głównych gałęziach przemysłu chemicznego do produktów nieorganicznych i organicznych. Zapakowane urządzenia kontaktowe, zarówno nieregularne, jak i regularne, są obecnie produkowane na dużą skalę w różnych firmach. Wiodące firmy w Europie to: Raschig, Sulzer, Nutter, Balke-Durr, Jamon itp.; w USA: Norton, Koch, Masstransfer, Glitch itp. Firmy te nie tylko uruchamiają przemysłową produkcję nasad, ale także prowadzą prace badawcze mające na celu udoskonalenie znanych konstrukcji nasad, opracowanie nowych konstrukcji, pozyskiwanie nowych, nowocześniejszych materiałów do ich produkcji itp.